A new case study from a textile fabrication company highlights the importance of choosing the correct bearing material for more efficient production.
A production line can only move as fast as the parts used to support it. Whether it is a conveyor system, a belt, or a sorting bin, using the right actuators, linear guide rails, and bearings will result in a more efficient manufacturing process. A recent case study out of Johannesburg, South Africa, highlights the need to implement proper support bearings for production. The company chose to change bearing materials after a recent shutdown to improve production and maintenance.
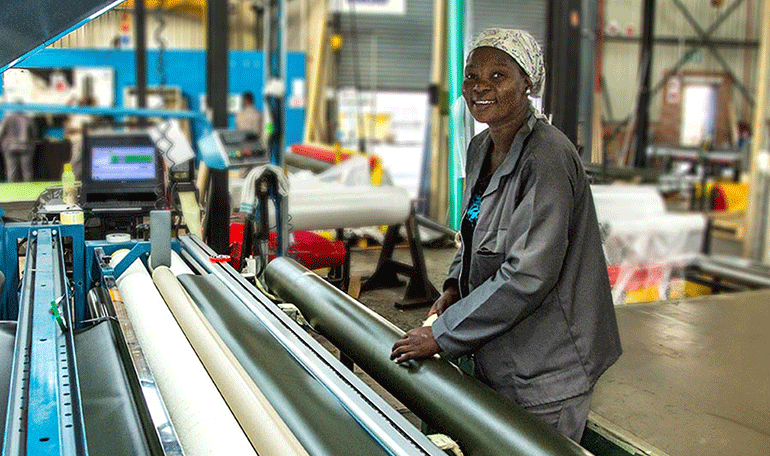
Arthur Dowson Ltd. is a laminating and coating factory that creates products such as dam linings, billboards, butchery aprons, upholstery materials, placemats, tents, tarpaulins, and jumping castle fabrics. The production process starts with the fabric roll shaft, with the raw material around it resting upon the support bearings. Once it receives the coatings on the one side, the material is rolled onto another fabric roll shaft supported at the other end of the production line, which is also supported by bearings.
The Arthur Dowson company laminates and fabricates different cloth materials, including upholstery materials, placemats, tents, and tarpaulins, using large fabrication rollers.
After that, 1000 meters of the roll is typically transported back to the start of the production line, so that the reverse of the material can also be coated. The process is then repeated, and the roll of fabric gains in weight and volume as it receives additional coatings. The fabric rolls can weigh up to two tons after coating, with some clients requiring more coatings that result in an even greater fabric weight.