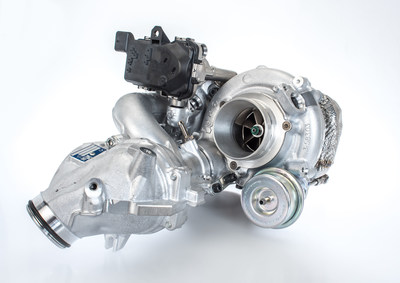
Most engineers didn’t go to school aiming to become economists, but that’s often what it feels like once you take on a managerial role. High-performance equipment is expensive, and downtime is costlier than ever.
Lubrication is a fact of life, as is maintenance, whether it’s an airliner on the ramp or a conveyor on an assembly line, and the overall cost of preventative maintenance is always in play. High temperature applications make the problem even worse. At 400° F and higher, conventional hydrocarbon lubricant formulations aren’t enough.
For the difficult environments found in aerospace and aviation applications, for example, high-performance perfluoropolyether (PFPE) lubricants can perform under extreme temperatures, pressures and exposure to harsh chemicals. Often, advanced PFPE lubes are the only solution, but what about cases where hydrocarbon formulations can survive? In this case, there are still strong cost and performance advantages to going with higher performance products.
Consider the true cost of lubrication in manufacturing.
Maintaining Lubrication in Extreme Environments
Machines can fail for any number of reasons, but improper lubrication is often a leading culprit. This is commonly due to environmental factors such as temperature, pressure or exposure to harsh chemicals, or due to a lack of scheduled maintenance and relubrication.
Extreme environments pose a significant challenge for keeping machines properly lubricated. Steam turbine controls, for example, will see wear on cam shafts, valve lift bar anti-friction bushings and gears if they’re using conventional lubricants, leading to excessive clearance, rough response and potential seizing of the governor control.
The result is an increased demand for re-lubrication, which in turn leads to increased maintenance efforts and costs. A major American supplier to the electric grid was forced to shut down its base load unit to repair and re-sleeve its bearings four times a year because the grease being used on the governor control valves was drying out.
Because the control valves were located unusually close to the turbine (10 feet, rather than the standard 30 feet), the company needed a grease that could handle the extreme temperatures the cam shaft bearings and fulcrum pins were exposed to on a daily basis.
The company opted for Krytox XHT-BDZ grease, which was able to withstand the high temperatures without evaporating. Since Krytox greases are designed not to oxidize or breakdown, replacing conventional lubricants with Krytox greases can improve turbine uptime and reduce operating expenses. In this case, the company was able to eliminate its quarterly shutdowns for maintenance.
Lubrication for Life
Although it’s true that proper lubrication is key to avoiding equipment downtime in extreme environments, any company can benefit from lower maintenance costs.
Cariboo Pulp & Paper has thousands of electric motors; so many that the mill was forced to run them without any re-lubrication process. Consequently, the motors typically lasted no longer than 4-6 years, with over 60 percent of breakdowns attributed to bearing lubrication failure.
Cariboo wanted to increase the life of these motors without having to implement a complex re-lubrication process. The experts at Chemours recommended Krytox AUT 2E45 as part of a “lubed-for-life” solution.
Inside the harsh environment at Cariboo Pulp & Paper. (Image courtesy of Chemours.)Over the next seven years, the mill began to cycle in bearings pre-filled with Krytox grease. In order to get the full benefits of the new grease, the mill had to completely remove the old hydrocarbon greases before adding the Krytox lubricant.
“If a customer tells us the Krytox isn’t working, nine times out of ten we find hydrocarbons in it when we test it,” said Chad Warriner, Technical Srvices Engineer at The Chemours Company. “If you mix Krytox with a hydrocarbon grease, you might be making your hydrocarbon performance better, but you lose all the performance gain of the Krytox.”
Avoiding hydrocarbon contamination requires more than just flushing out your old lubricant. “You can use Krytox in a standard grease gun,” said Warriner, “But we would recommend changing the Zerk fitting to a different size that won’t fit on your other grease guns, because you don’t want someone putting a hydrocarbon on top of the Krytox. We also recommend tagging your equipment, as well as changing the fittings.”
After successfully converting the bearings in more than 100 motors to Krytox lubricants, Cariboo has not had a single bearing failure, nor has it needed to replace any electric motor using Krytox AUT 2E45 due to lubrication issues. Cariboo expects to more than double the lifetime of its electric motors, in addition to saving on costs by avoiding implementing a complete plant-wide re-lubrication process.
PFPE – Not Just for Harsh Environments
Steam turbines and electric motors in a pulp and paper mill present significant challenges for lubrication, but there are benefits to using a high-performance perfluoropolyether lubricant in almost any application.
Some manufacturers may want to run a motor for two or three times the normal re-lubrication cycle, pushing it to its limits in order to produce as many parts as possible before having to shut down. Of course, in these high-pressure situations, the cost of missing a re-lubrication cycle can end up being even higher.
For this reason, a high-performance grease with a long lifespan may be preferable to a less reliable alternative with a lower upfront cost. “If you miss a lubrication cycle, Krytox is going to keep working,” said Warriner. “The ingredients are not going to break down, so you’ve got some insurance.”
These two greases were placed in an oven at 450° F for 40 hours. The hydrocarbon grease lost 40 percent of its weight and developed tar. The Krytox PFPE grease remained unchanged in weight an appearance.
Krytox greases see a wide range of applications because of their flexibility. “They’re non-flammable, they don’t outgas and they have a very good toxicity rating,” said Warriner. “We have food-grades, many that are H1-approved, which can also be used. Krytox also doesn’t oxidize, so there’s no tars and it doesn’t coke up like a hydrocarbon grease would.”
Although you can use Krytox in many of the same applications as hydrocarbon greases, it’s important to note that the two types of lubricant are graded in different ways.
“The oil viscosity is the same—it’s still represented in centistokes—but the end-user needs to be aware that our density is twice that of hydrocarbon,” said Warriner. “So, if you’re used to filling bearings by weight, you have to be careful you’re not putting in half as much grease. That’s why you should fill the bearing by volume.”
Because of the higher traction coefficient and thicker film build, Krytox will see slightly higher temperature increases, though Warriner argued that this should not be a cause for concern: “Since it doesn’t oxidize, the Krytox grease doesn’t really care about that. Plus, you’re only talking about a couple of degrees anyway.”
If you’re uncertain about whether or which Krytox grease is best for your application, the experts at Chemours can help. “We actually have a full-service tech service team that can do webinars or talk things through face-to-face,” said Warriner.
In manufacturing, as in life, the most expensive solutions aren’t necessarily the best ones; but in some cases—like lubrication—you really do get what you pay for. In addition to reducing downtime due to lubrication failure and cutting down on maintenance and relubrication cycles, there are other benefits to using high-performance PFPE lubricants.
For example, if you don’t have to re-lubricate a bearing while the line is running, you also don’t have to guard it, reducing costs. Industrial applications that specify Krytox lubricant as a factory fill can give a process or manufacturing engineer extra flexibility if a motor or bearing doesn’t need frequent access by a technician. Savings are possible through a smaller footprint, and in some applications, a smart engineer may be able to achieve a lube life that exceeds the equipment’s run life, eliminating lubrication from the PM program for that unit.
Savings of this kind aren’t always obvious—especially not to accountants—but those in the know can recognize the benefits of switching to a high-performance PFPE lubricant.