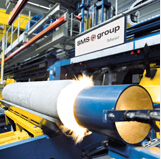
Evolution and alternatives to boron nitride
Manufacturers of aluminium sections rely on a number of technical substances in their production plants. To satisfy this demand, Klüber Lubrication offers a portfolio of release agents and lubricants that is continuously adjusted to the changing requirements of extruder operators.
A crucial application is the lubrication of the extruder ram where it is in contact with the preheated billet. The focus is on the release effect, while a lubricating effect is required only for the micromovements in the contact zone.
From graphite-based greases to boron nitride
Over many decades, graphite-based greases were used as a "rudimentary" solution, and still are in some cases. They have the disadvantage of high consumption volumes, resulting in a heavily contaminated machine periphery.
A bit more advanced, yet not quite state-of-the-art, is the use of so-called "graphite candles", i.e. solid lubricant sticks based on wax, containing oil and graphite, which are molten for application onto the billet. Similarly, graphite suspensions may be sprayed onto the contact surface.
For approximately 20 years, boron nitride has been well established on the market, enabling considerably lower consumption volumes. It comes in the form of a powder requiring electrostatic charging for uniform adhesion to the surface. Newer extrusion presses are often fitted with an electrostatic powder application appliance, either as standard or as an option. Furthermore, over the last few years, we have also seen a trend towards, and specific customer requests for, light-coloured, aqueous release agents. Most such products available on the market today are based on technical salts or boron nitride as an active ingredient.
Boron nitride is not the only option
While Klüber Lubrication has a sound portfolio of the "conventional" products described above, we have for several years been focusing on a powdered product whose chemical composition is fundamentally different. This product is a special mixture of phosphates and silicates. It is a powder enabling lower consumption and can be chosen as an alternative to boron nitride products. It can also be applied in an electrostatic process and is available at a competitive price.
Klüber Lubrication is currently developing an aqueous version of this powder. We will be pleased to conduct application studies in cooperation with interested extruder operators. If you are interested, please e-mail to: Alu-extrusion@klueber.com
Extrusion moulding: a widely used process
Extrusion moulding is a widely used massive forming process. It involves an aluminium billet being heated to a temperature between 450 ° and 500 °C, depending on the specific alloy used, to make it sufficiently ductile. The billet is pressed into the tool by means of a hydraulically operated ram (the largest presses exert a pressure of 150 MN), forcing it through the die on the other side to give it the desired shape. A release agent is required to prevent the aluminium billet from welding onto the ram.